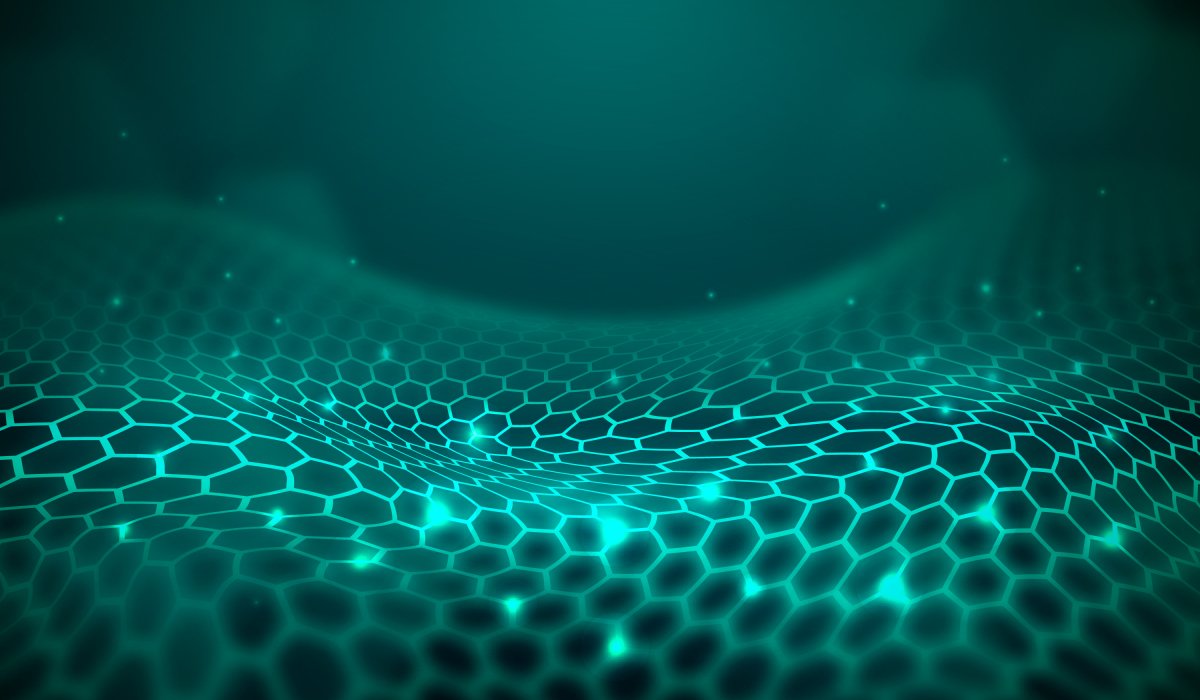
Powłoki narzędziowe, powłoki PVD
Nowoczesne powłoki narzędziowe
Zużycie narzędzi spowodowane ich ścieraniem generuje w przedsiębiorstwach ogromne koszty. W celu ograniczenia ich eksploatacji coraz częściej wykorzystuje się technologie powierzchniowe w postaci specjalistycznych powłok. Pozwalają one na zwiększenie twardości narzędzi i wydłużenie ich czasu pracy. Dodatkowo umożliwiają pracę w ekstremalnych warunkach (temperatura, ciśnienie) gdzie ich bardzo szybkie zużywanie powodowałoby bardzo wysokie ceny wyrobów końcowych.
Zalety stosowania powłok narzędziowych
Stosowanie powłok narzędziowych wpływa korzystnie nie tylko na wydajność pracy narzędzia ale także na poprawę jego właściwości.
Zalety wykorzystywania powłok narzędziowych:
- poprawa właściwości mechanicznych – zwiększenie twardości, odporności na ścieranie, wydłużenie pracy narzędzi
- zmniejszenie współczynnika tarcia – wolniejsze zużywanie się narzędzi, oszczędność energii w procesach produkcyjnych
- ochrona przed korozją – możliwość stosowania narzędzi w środowiskach wodnych, chemicznych
- poprawa estetyki narzędzia – poprawa wyglądu, istotna w przypadku np. branży automotive
Metody nanoszenia powłok narzędziowych
Istnieje wiele rodzajów metod nakładania powłok narzędziowych. Ich wybór uzależniony jest od wymagań dotyczących trwałości, zastosowania narzędzia, procesu produkcyjnego czy dostępnego budżetu.
Najczęściej powłoki nanoszone są metodami PVD i CVD.
PVD (Depozycja fizyczna z fazy gazowej) to proces polegający na kondensacji pary materialnej w postaci cienkiej warstwy na powierzchni narzędzia w warunkach próżniowych. Stosowane wszędzie tam gdzie wymagane jest zwiększenie odporności na zużycie, zwiększenie trwałości i poprawa właściwości antykorozyjnych. Najczęściej wykorzystywane dla narzędzi tnących, form wtryskowych, narzędzi chirurgicznych, elementów dekoracyjnych.
CVD (Depozycja chemiczna z fazy gazowej) to technologia w której cienka warstwa materiału osadzana jest na powierzchni narzędzia poprzez reakcję chemiczną gazów reakcyjnych. Poza zwiększeniem trwałości narzędzia, odpornością na ścieranie czy poprawą odporności na korozję metoda ta zwiększa także przewodność elektryczną. Wykorzystywana jest dzięki temu przy procesie produkcyjnym półprzewodników. Dodatkowo również na narzędzia tnące, powłoki optyczne, elementy dekoracyjne.
Do nanoszenia powłok stosuje się również wiele innych metod, między innymi: powlekanie, napylanie termiczne, osadzanie chemiczne czy plazma powłokowa.
Rodzaje powłok narzędziowych
W zależności od wymagań procesu produkcyjnego i stosowanej metody nanoszenia wykorzystuje się różne powłoki stosowane na powierzchniach elementów. Jest wiele rodzajów powłok występujących na rynku. Większość firm stosuje swoje wewnętrzne nazwy i oznaczenia. Najczęściej wykorzystuje się wariacje poniższych pierwiastków:
- powłoki DLC – wykorzystują węgiel w celu uzyskania zbliżonych właściwości do diamentu, powłoka jest twarda, odporna na zużycie, ma niski współczynnik tarcia, stosowana na narzędzia w wymagających warunkach pracy
- powłoki TiN – nadają odporność na ścieranie, korozję i redukują tarcie, stosunkowo tanie w nakładaniu
- powłoki TiCN – wyjątkowo odporna na zużycie, twardość, niski współczynnik tarcia
- powłoki AlTiN – bardzo wysoka twardość, idealne do stali nierdzewnych, oraz takich które trudno obrabiać, stosowana na narzędzia medyczne
Zapraszamy do współpracy w zakresie spawania MIG/MAG/TIG, automatyzacji przemysłu oraz projektów maszyn.
Kontakt znajdziesz tutaj - Dane kontaktowe
Więcej szczegółów odnośnie naszej bieżącej oferty uzyskasz w formie unikalnej wideoprezentacji - Prezentacja LucasTech do zobaczenia której serdecznie zachęcamy.